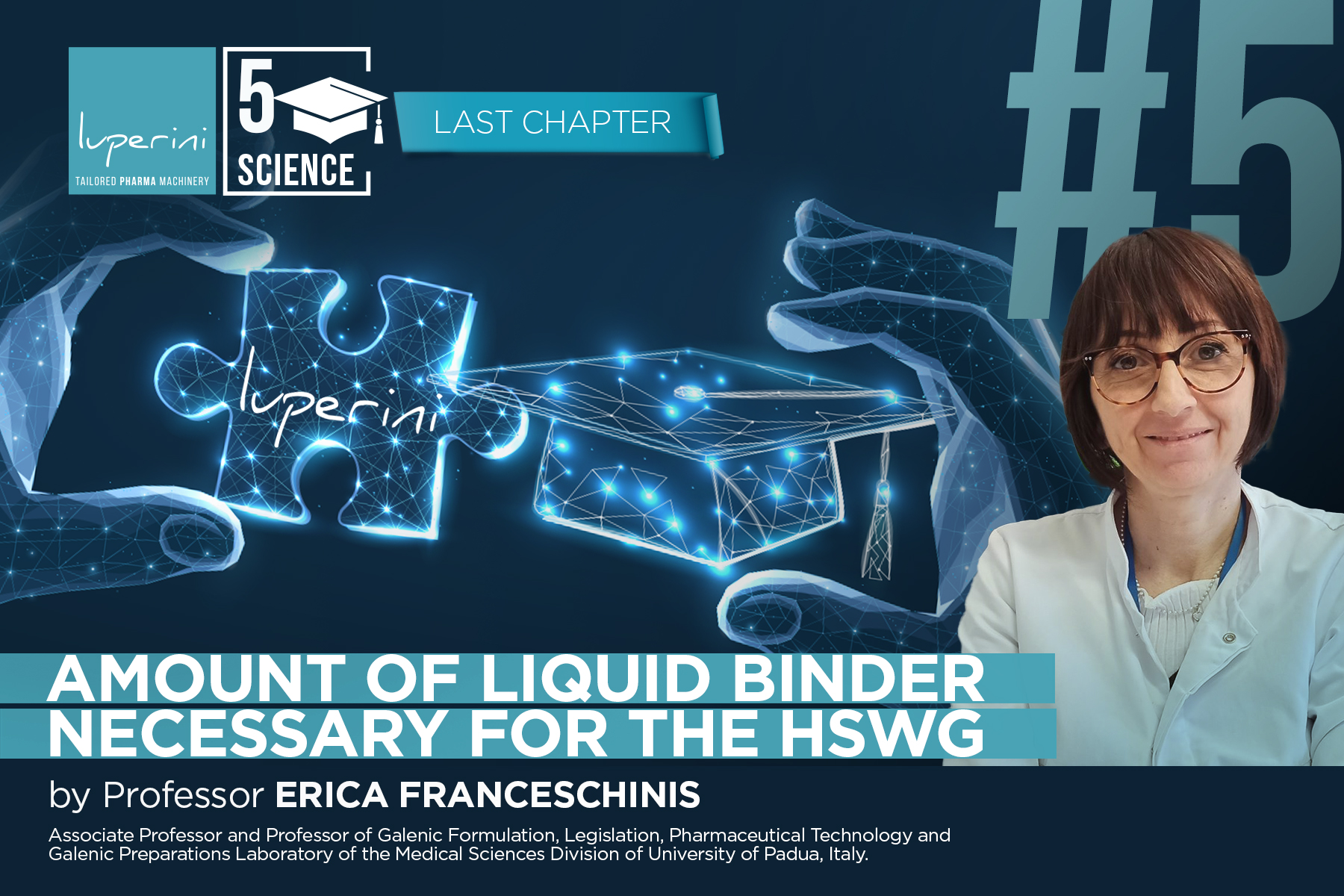
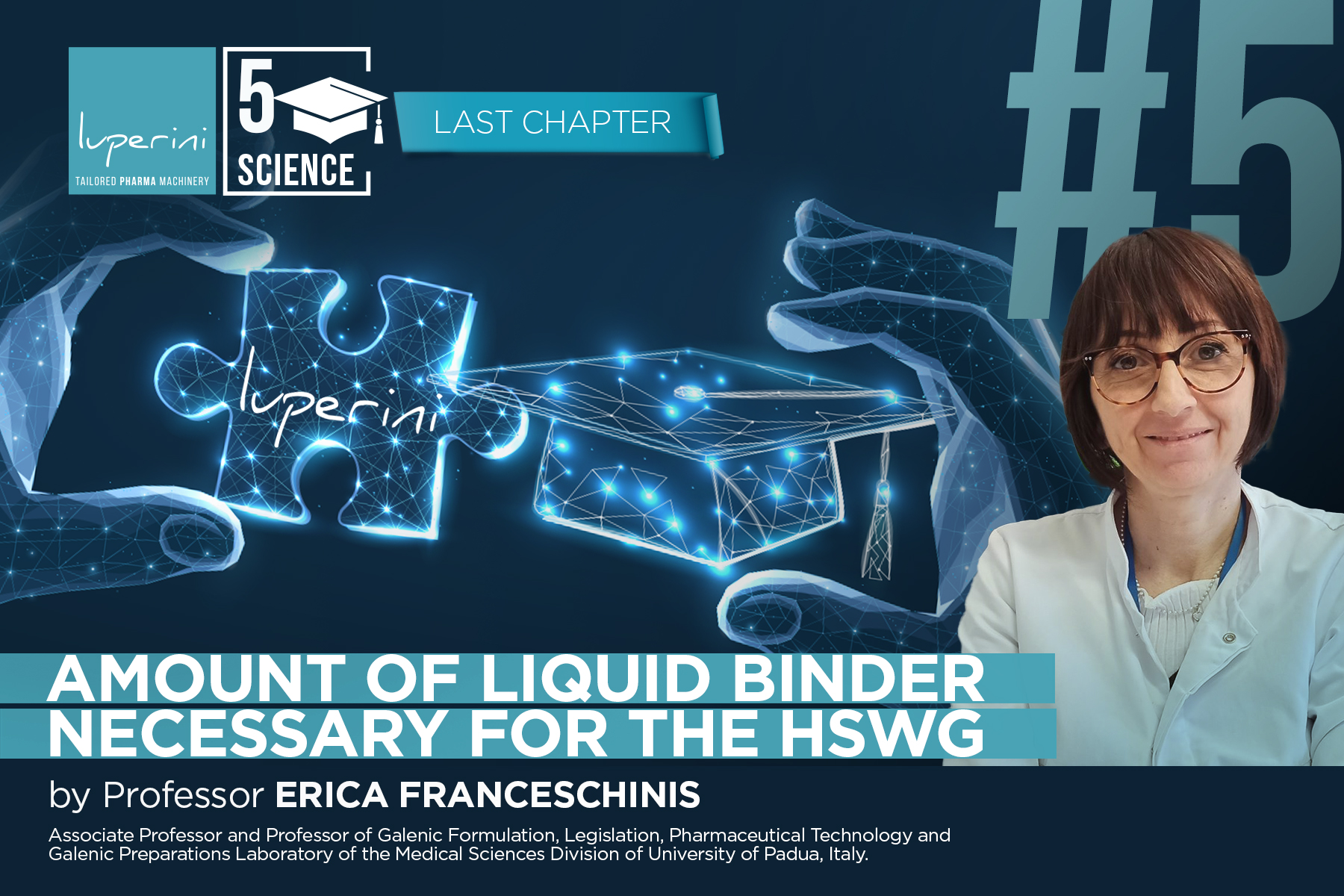
In the final chapter of Luperini Science, written by Professor Erica Franceschinis (Associate Professor at University of Padua-Italy), we explore how automation can overcome traditional approaches in granulation processes. Available in English, Luperini Science Chapter 5 is a practical guide to production processes optimization using specific technologies.
Amount of liquid binder necessary for the HSWG
Liquid bridges represent the main forces involved in the formation of the wet granule structure. When the granulating liquid is added to the formulation, it gradually penetrates the powder bed, filling the voids between the particles that are initially connected to each other by the formation of liquid bridges. The subsequent addition of liquid leads to gradual filling of the voids until a slurry is formed. Depending on the amount of liquid added, the powders experience different capillary saturation states. The saturation states are called pendular, funicular, capillary, and slurry states and are represented in Fig. 1. The optimal amount of liquid binder necessary to perform the wet granulation process in a high shear mixer is that which allows transition from pendular to funicular state.
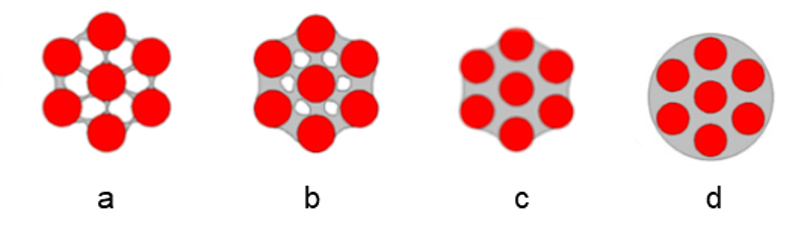
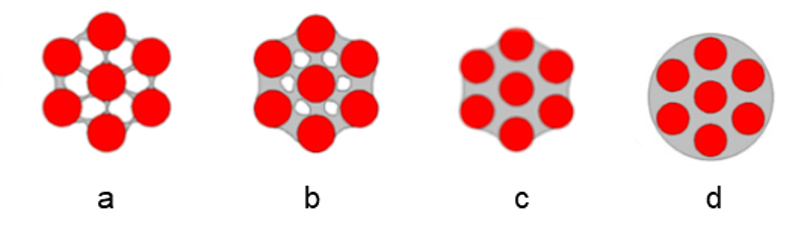
The optimal amount of liquid binder is still often evaluated through an empirical assessment defined as hand squeeze test. This assessment consists of squeezing a sample of wet powder into a fist. The amount of liquid is optimal if the squeezed wet mass maintains a compacted shape after the disclosure of the fist and presents some breakages (Fig. 2). This approach is also used as an in-process control for high-shear granulation. This method is not reliable as it is hugely affected by the experience and the sensitivity of the operator.
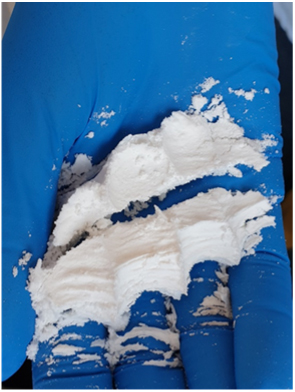
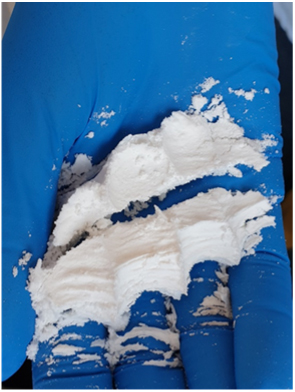
To conduct a systematic assessment, it is possible to equip the granulator with potentiometers, ammeters, or torque meters to monitor electrical or mechanical parameters associated with the granulator’s motor or impeller movement during the addition of liquid binder and the evolution of the process. The measured parameters are generally the torque recorded by the impeller of the high-shear mixer or the adsorbed power of the engine.
An example of the shape of torque profile registered during the addition of the liquid binder to the powders inside a high shear granulator is reported in Fig. 3.
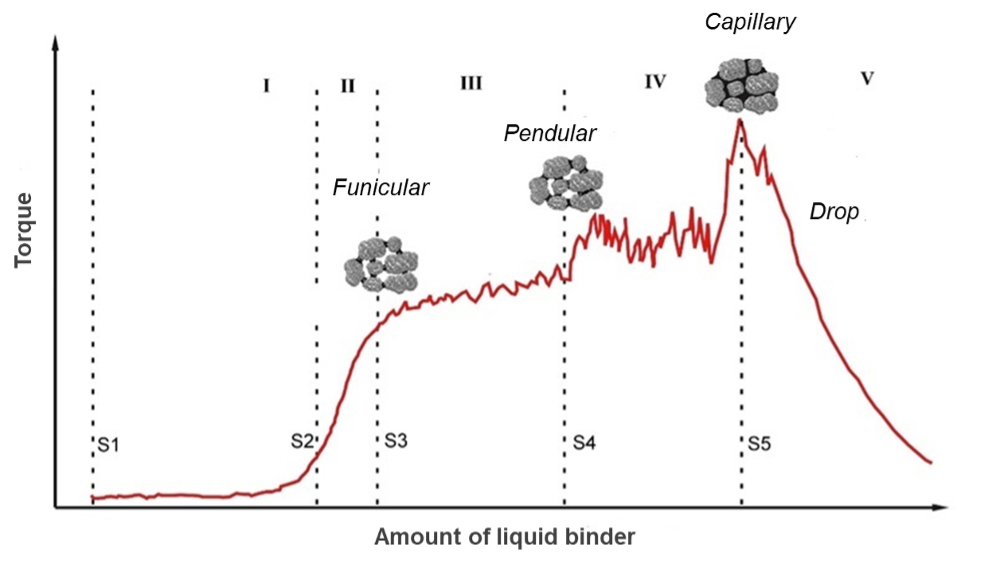
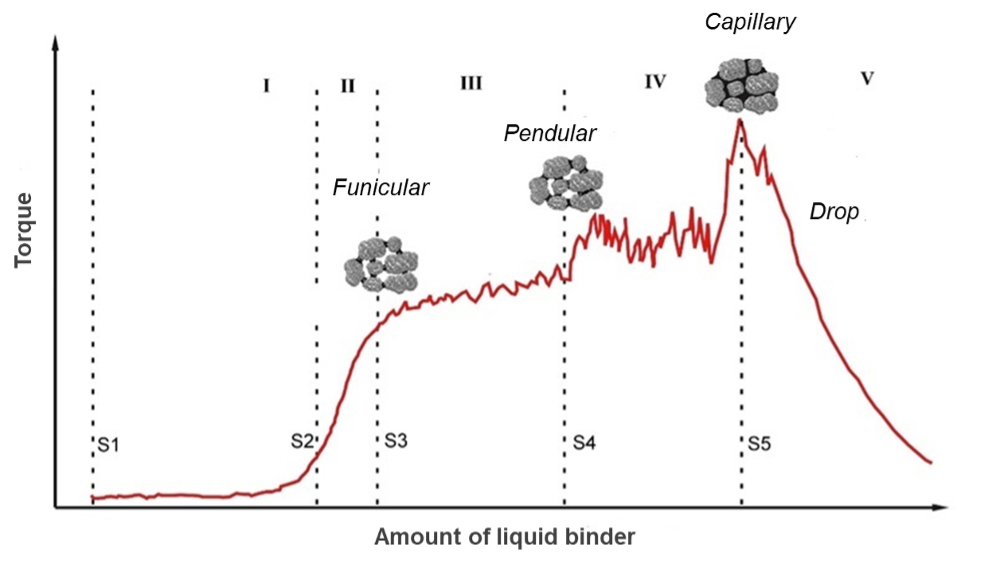
The torque profile can be divided into five sections:
S1 corresponds to the wetting of the powder. In this phase only the initial bridges between the primary particles are formed.
S2 a rapid increase of the torque values is observed; this phase corresponds to the achievement of the pendular saturation state.
S3 corresponds to the transition between the pendular and funicular saturation states. This transition is represented as a plateau of the torque profile.
S4 represents the filling of the pores between the particles and the achievement of the capillary state.
S5 represents the drop phase characterised by a drop in mass resistance.
The identification of the different liquid saturation states of the mass on a high-shear mixer opened the way to the use of the torque recorded during the process to identify when the amount of liquid added is sufficient to perform the granulation, thus avoiding the hand squeeze test.