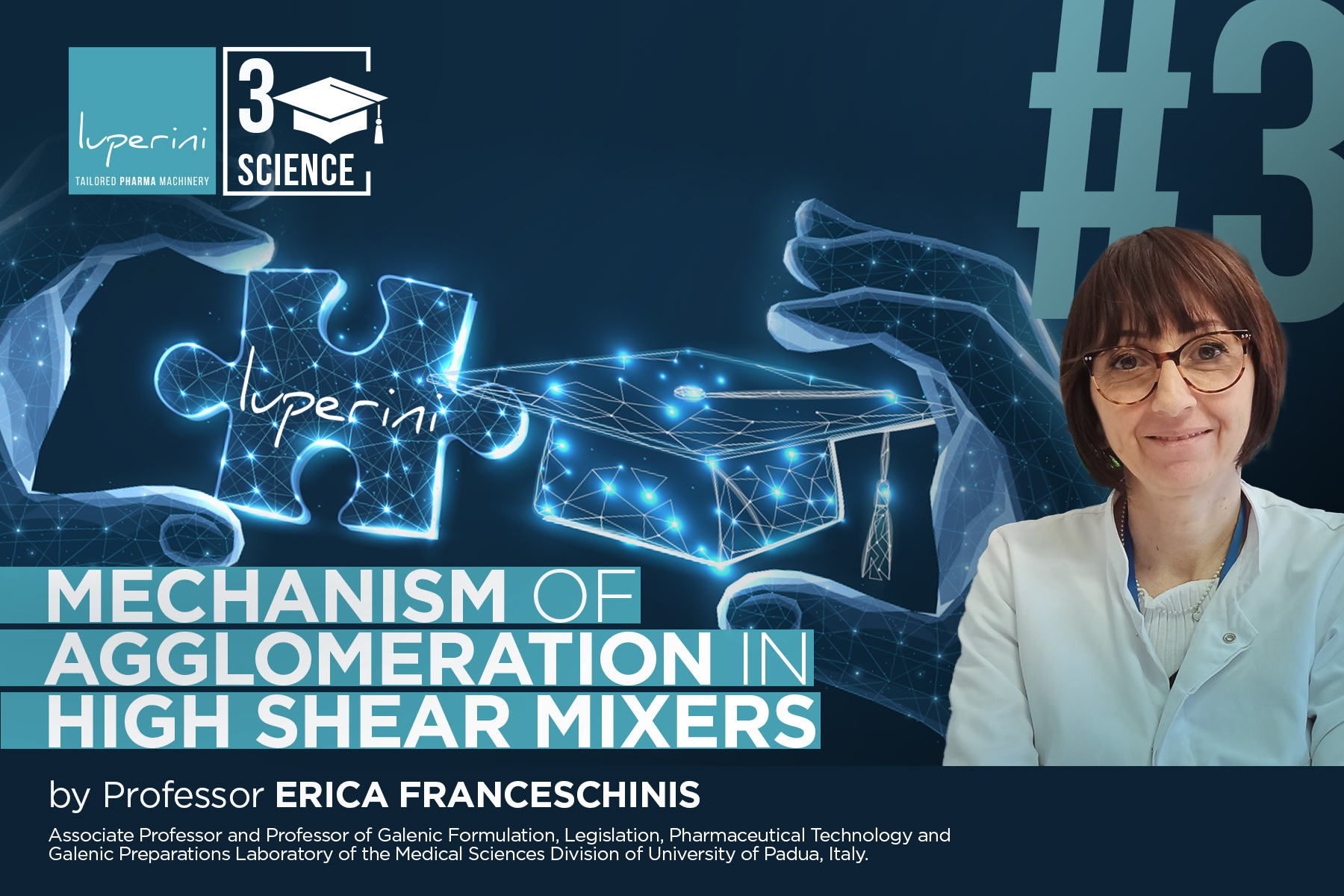
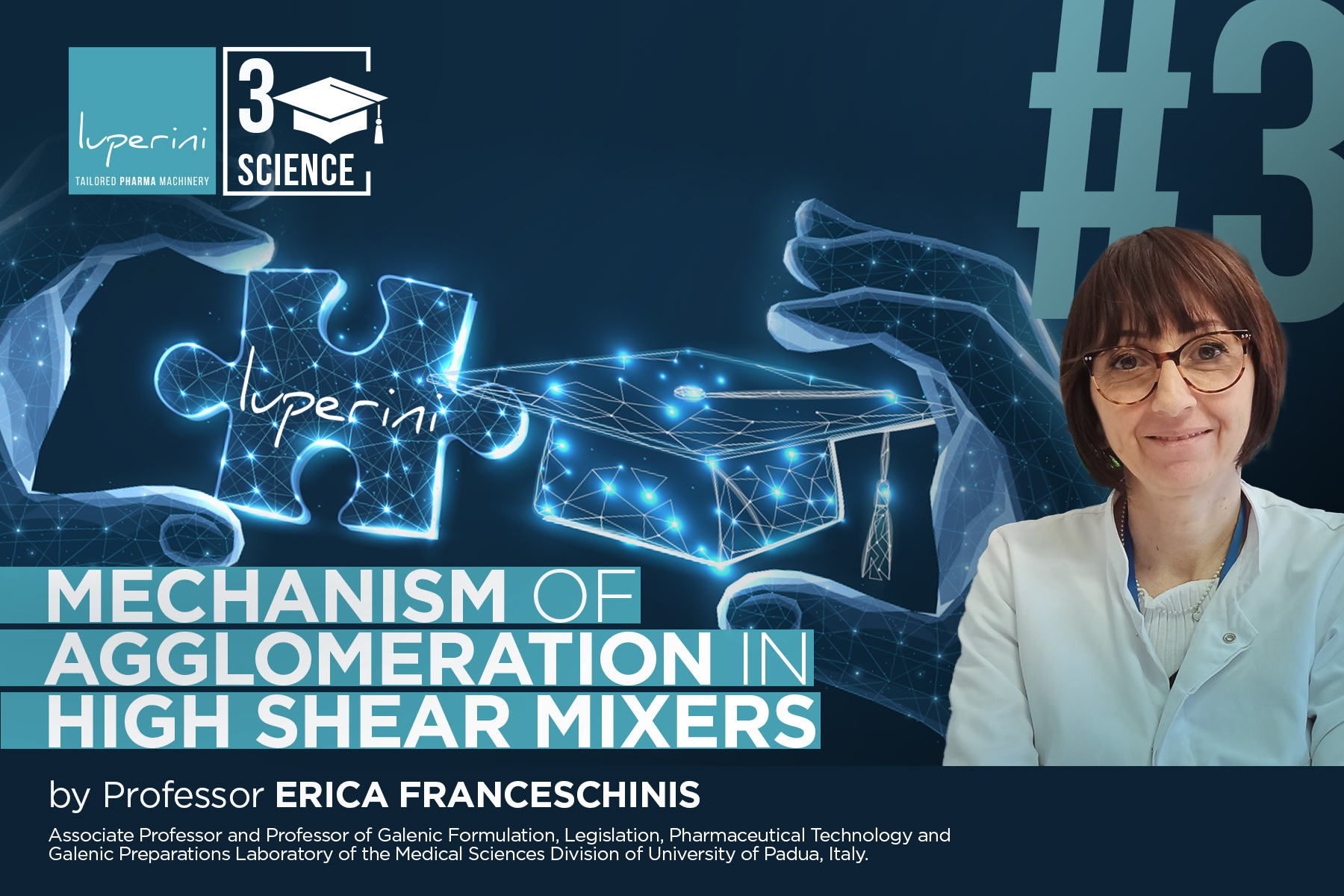
It is our pleasure to share the third chapter of the important scientific collection “Luperini Science”, promoted by Luperini Tailored Pharma Machinery, in collaboration with Professor Erica Franceschinis -University of Padua, Italy-. This contribution has the ambitious objective of providing users with a periodic instrument of scientific information on the process and technologies for granulation applied to the pharmaceutical industry, thus, contributing to training operators in the sector who, following the chapters of this important section, will have access to relevant information to optimize production processes.
Mechanism of agglomeration in high shear mixers
During agglomeration and granule formation, three separate phenomena take place simultaneously:
- Wetting and nucleation: where the liquid binder is added to the powders and distributed through the powder bed leading to nuclei formation.
- Consolidation and growth: where collisions between granules and between granules and the equipment lead to the agglomerate growth and densification.
- Attrition and breakage: where the impact of the granules between each other or with the equipment leads to their breakage.
Wetting and nucleation are the phases in which there is the first contact between the formulation powder and the granulating liquid. The liquid interacts with the powder to form the liquid bridges that lead to the formation of the nuclei. These nuclei are identified as the original particles, which will turn into granules in the following phases because of their coalescence and further consolidation. Thermodynamics of wetting depend on the contact angle between the liquid binder and the powder bed and on the spreading coefficient. To obtain an efficient wetting phase, it is important to have a low contact angle value and a positive spreading coefficient.
This initial phase is particularly critical; in fact, several authors pointed out how the formation of nuclei could be affected by the dimensions of the drops of the liquid binder and by the influence of some process parameters (e.g. the renewal of the powder bed and the flow rate of the liquid binder flow rate). These will lead to the formation of different nuclei, which will influence the properties of the final granules, mainly in terms of the particle size distribution. In particular, the optimal situation is represented by the ability of the single droplets to penetrate the powder bed and immediately form nuclei without any coalescence with other droplets. This is possible when the droplets of the liquid binder are small and penetrate in the powder bed sufficiently fast, while the surfaces of the powders are constantly renewed.
In the growth and consolidation phases, the coalescence between the nuclei takes place leading to the formation of bigger agglomerates. Coalescence is due to the deformability of the particles involved, given by the presence of liquid that provides the plasticity of the wet mass.
Granules grow until the equilibrium between the coalescence and rupture of the agglomerates is reached. Granules consolidate due to collisions between them and with the wall of the bowl. This consolidation decreases the porosity of the granule and increases the density of the granule.
On the basis of granule deformability (expressed as Stokes’ deformation number) and the amount of liquid binder (expressed as maximum pore saturation) different growth regimes were identified.
The crumb regime is characterised by a wet mass with high deformability. This regime leads to the formation of irregular granules which do not grow because of the low resistance of the wet mass.
In contrast, in the induction regime, the wet mass presents a high resistance to kneading and a low deformability. In this case, the growth shows a characteristic trend. The nuclei show an initial lack of growth, and they consolidate without coalescing with each other. Subsequently, the high consolidation leads to the movement of the liquid binder from the internal pores to the surface of the nuclei that promotes exponential and uncontrollable growth, leading to lump formation.
In the steady growth regime, the wet material presents an intermediate and optimal deformation, which leads to the coalescence of the nuclei. This produces a constant growth of the granules until the equilibrium is reached. The diameter achieved at equilibrium depends on the amount of liquid used, the components of the formulations, and the impeller speed.
The phases of attrition and breakage take place from the very beginning of the process and are due to the shear applied to the granules. However, in the first stage of granulation, growth and consolidation phenomena prevail, leading to granule growth. As the granules grow, the breakage phenomena gain importance and an equilibrium between growth and breakage is reached. The final size of the granules will depend on the formulation and process parameters.